鉄鋼材料の熱処理と表面処理の基本 第3回 熱処理と表面処理の実際
技術士の奥野先生に「鉄鋼材料の熱処理と表面処理の基本」について全3回で連載いただきます。第3回は、熱処理と表面処理の実際についてです。
鉄鋼材料は、熱処理を行なって使用するのが基本となる素材であり、固体で相変態を起こす鉄の特性を最大限に生かすため、他の金属素材よりも熱処理の種類は多く複雑になっている。しかしながら、熱処理は特殊工程(=その処理を実施したかどうか、製品を見るだけではわからない工程)とも呼ばれ、実務上、最適な熱処理を選択し、かつ決められた通りに行うことも難しい。
本稿では、最適な熱処理方法を選択するための考え方、および、熱処理起因のトラブルの解決策を紹介しながら、熱処理の実務として押さえておく必要のあるポイントを概説する。
目次
1.熱処理と表面処理は「鋼の肝」
(1)鉄鋼材料は必ず熱処理を行なってから使用する
鉄鋼材料は、すべての素材に熱処理をして使用する。SS400のように、熱処理不可と言われる素材もあるが、これは、製品を使用する立場での見方であり、その素材を製造する時点では、熱処理を行なっている。このため、このような素材は「使用時には」熱処理ができない、というのが正しい。
また、鉄鋼材料は熱処理の種類が非常に多い。これは、鉄が固体で相変態を起こすこと、オーステナイトからフェライトに変わること、また、炭素を含みマルテンサイトやベイナイトなど、さまざまな組織を持ち、これらの組織の特性を活用していることによる。
通常使っている鉄鋼材料は、20000MPaとも言われる理論強度の遥か下、数百〜数千MPaの強度で使われることがほとんどであるが、理論強度に達しない要因は、素材の中には、転位などの格子欠陥、表面疵、介在物などが存在するためであり、これらの欠陥をできるだけ少なくすることも熱処理の目的の一つとなる。
(2)日本独特の鋼種体系:マンガン鋼とボロン鋼
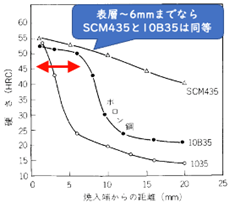
【図1】10B35の焼き入れ曲線
鉄は様々な元素を添加することによって特性が変わり、歴史的には、最初は経験から、そして、そのメカニズムを調べて明らかにする歴史を経て、さまざまな合金鋼が生み出されてきている。
この中で、Mn系(Mn-Cr系を含む)は日本独自の鋼種系であり、海外では規格化がなされていない。(逆に、海外で規格化されていて日本で規格化されていないものに窒化鋼がある。後述(4)項を参照)日本においては、このMn系の材料は、ボロン鋼の素材として自動車部品用途を中心に多用される。
例として、クロムモリブデン鋼SCM435を焼き入れして使用する場合、SCM435の代替としてボロン鋼SAE 10B35が使用できる。(注:1035Bと、Bが後置される呼称もある)焼き入れ曲線を比較すると(図1)、表層から6mm程度であれば同等の強度を持つため、表層部分だけ焼きが入れば良いような製品特性であれば、安価なボロン鋼を、高価なCr・Moを含むSCM材に代替できるため、素材のコストダウンに寄与する。
(3)浸炭処理の実際と肌焼き鋼
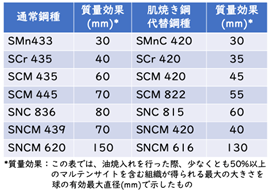
【表1】肌焼き鋼の質量効果
鋼種によって質量効果(=焼きの入り方)にどの程度に差があるかを比較したものを表1に示す。数字が大きいほど焼きが入りやすい鋼種だが、それぞれ対応する肌焼き鋼があり、いずれもカーボンの含有量が少なく、焼きの入り方も小さくなっている。
これらの肌焼き鋼は、通常浸炭処理によって表層を硬くして用いられることから、肌焼き鋼を使うことで炭素量を減らし、コストだけでなく素材の強靭性を高める目的で使われる。
浸炭処理の適用に関しては、上記以外に以下の3点のポイントを押さえる必要がある。
①構造用鋼程度の化学成分範囲では鋼種による浸炭性には差がないため、材料は焼き入れ性で選ぶ。
②苛酷な条件で使われる部品に対しては、Ni-Cr-Mo鋼またはNi-Mo鋼を選ぶ
③1000℃超の高温浸炭では結晶の粗大化を生じるため、これを防止するために、Nb添加鋼を用いる。
(4)窒化用素材の選定
窒化用の素材選定に際してのポイントは以下の3点となる。
①窒化は変態点以下の温度域の処理のため、完全な焼き入れ焼きもどし組織が得られる鋼種を選ぶ。
(焼き入れ焼き戻しをしてしまうと、その材料の特性が失われてしまうような素材は避ける)
②窒化温度域がちょうど高温焼戻し温度域になるため、素材の軟化抵抗の大きさも考慮する。
③窒化による硬化を生かすために、Al, Cr, V, およびMo等が添加された素材を選ぶ。
通常広く使用されているSCMやSNCMなどの構造用合金鋼を窒化することでは、十分な強度を得ることができないが、JIS規格鋼には窒化用の鋼として規格化されているものがAl添加鋼しかない。海外規格では窒化用鋼としてCr添加鋼、Mo添加鋼があり、国内の特殊鋼メーカーでも独自規格としてラインアップされているので、窒化処理用としては、JIS規格にこだわらずに材料を選択する必要がある。
(5)高周波焼き入れの実際
高周波焼き入れについては、以下の2点を考慮して素材を決める。
①硬さは炭素量だけで決まり、合金成分には依存しない。
②焼き入れの深さは、合金成分に強く依存する。実用的には、C系→Mn系→Mn-Cr系→Mo系の順番
に焼き入れ深さが大きくなるので、必要に応じて焼き入れ性の良い材料を選べば良い。
2.焼き割れと冷却速度
焼き割れは、冷却による収縮と、マルテンサイト変態による膨張が同時に起こることで発生する。このため、焼き割れを防ぐためには、マルテンサイト変態開始温度以下を緩やかに冷却する、というのが基本となる。水は、冷却のために最も広く安価に利用される媒体であるが、水による冷却の特性を理解することは重要である。
(1)マルテンサイト変態開始温度の推定
マルテンサイト変態開始温度(Ms点)は、素材の化学成分をパラメータとする推定式が複数提案されており、これらの式に当てはめて検討すると良い。おおむね、200〜290℃程度の温度となる。
(2)沸騰曲線
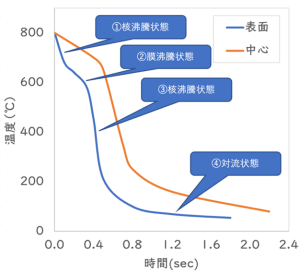
【図2】沸騰曲線の例
水は冷却媒体として非常に優れている。水による冷却のメカニズムには対流、核沸騰、膜沸騰と呼ばれる3つの現象があり、冷却効率が高い順番に並べると、核沸騰、膜沸騰、対流となる。高温状態では膜沸騰が支配的になり、核沸騰はより低温にならないと発生しない。
沸騰曲線の例を図2に示す。冷却開始直後は核沸騰状態になり急激に冷却が進むが、ごく短時間で膜沸騰状態に移行し、冷却速度は大きく下がる。500℃台まで下がると、水蒸気の膜が消失し、核沸騰状態に移行するため、冷却速度は一気に上がる。この状態は沸騰状態がなくなる100℃近辺まで続き、以降は対流冷却となる。
すなわち、普通に水焼き入れを行い常温まで冷却すると、200〜290℃の温度域は非常に速く通過してしまい、徐冷の条件が満たせなくなってしまう。実操業では温度を見ながらコントロールすることは難しいため、テクニックの一つとして、冷却開始から時間を決めて焼き入れを行う「時間焼き入れ」が適用されることもある。
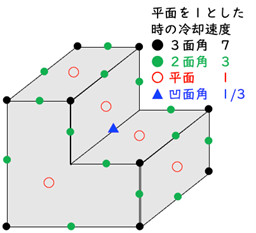
【図3】形状による冷却速度の差
冷却速度は製品の形状によっても影響を受ける。特に複雑な形状の製品の場合は、図3に示すように、場所によって冷却速度が20倍程度異なる場合もあることに留意する。
(3)焼き割れの防止
焼き割れは、焼き入れ時の冷却速度が適正でなかったことに起因する不具合であり、製品のかなり大きな部分に割れが生じるため、製品廃却となる可能性も高く、また、見逃せば大事故につながる危険性もあるため、慎重に検出しなければならない。
冷却速度が適正とならない要因としては、製品の形状や肌荒れ、焼き入れを行うまでの加熱処理、焼き入れより前の熱処理の状態など多岐にわたる。多くの場合、原因は一つではないため、QC手法を用いて要因を特定し、それぞれに対策を講じることが必要になる。
浸炭材は、表面の炭素量が多いため、焼き割れにはより注意が必要である。炭素量が高いと、Ms点が低くなることに加え、Ms点が、芯材と表面で異なることにも注意する。
3.疲労破壊、遅れ破壊、研削割れ
(1)特性要因図の活用による原因の深掘り
金型の摩耗や破損について、その原因を明示した特性要因図の一例を図4に示す。
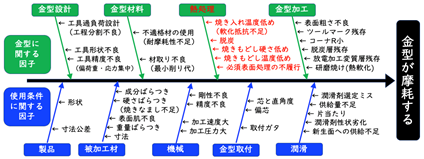
【図4】金型の摩耗に関する原因(特性要因図)
この図は金型の摩耗について書き出したものだが、金型は、熱処理を行う製品としては最も厳しい環境で使われることから、記載の項目、分析された要因はそのまま、他の金属材料の不具合の要因分析に使うことができる。熱処理に起因する不具合であっても、熱処理そのものではなく、それ以外の要因も検討すべきである、ということを教えてくれる。
(2)ヒートショック(熱疲労)
金型鋼の損傷として最も多いのが、ヒートショック(熱疲労)であり、高熱かつ高荷重環境で繰り返し使用されることによって発生する。加熱時、表面は熱膨張によって圧縮されるが、冷却の際には逆に引張応力が生じ、この繰り返しによって、表面にある微細な傷や割れを基点にして広がる、というのが基本的なメカニズムとなる。
このヒートショックは、程度の差こそあれ、ほぼすべての金型鋼に発生する。高温、高荷重レベルほど発生しやすくはなるが、素材として硬ければ良いというものではない。製造の際には、金型部位による差が出ないよう均一に熱処理を行うことが基本となるが、形状が複雑であるため実際には困難であり、損傷が発生しやすい部分だけを強化する手段もとられる。まずは、決められた通りに熱処理が出来ているか、を確認することが基本的なポイントである。
(3)疲労破壊
材料が破壊するトラブルは、その半数以上は疲労破壊が原因である。疲労とは、変動応力の繰り返しにより発生するものであり、素材としては、疲労強度を向上させることが必要であるが、疲労強度が高くなると、延性や靭性が低下し、微細な材料欠陥から微小な亀裂が入りやすくなる(つまり、脆くなる)ため、素材としての疲労強度の向上には限界がある。
実務上の疲労強度改善の方策としては、①疲労破壊の起点部になりそうな部分を極力無くす、②脱炭層が生じないように、生じた場合は表層研削を行う③形状的に応力が集中しそうな場所に対して、高周波焼き入れ、レーザー焼き入れ、ショットピーニングの適用を検討すること、などが挙げられる。
(4)遅れ破壊
遅れ破壊は、一定の静的荷重がかかっている状態、かつ、水分が存在する場合に発生する不具合で、ボルトやネジなどの締結部材に発生することが多い。また、遅れ破壊は、水素脆性割れとも呼ばれる。
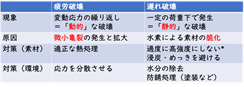
【表2】疲労破壊と遅れ破壊の比較
遅れ破壊は疲労破壊とよく似ているが、原因が異なる(表2)。遅れ破壊の対策は、水分の侵入を防ぐことと、水素脆性を抑えることの2点である。鉄鋼は高強度になればなるほど、水素脆性が顕著になることから、JIS規格でも、ボルトの強度には上限がある(1000MPa級まで)。また、脱炭層の存在も水素脆性を促進するため、浸炭処理およびリン酸塩のメッキ処理も避ける。
リン酸塩のメッキについては、通常熱処理前の加工工程で、潤滑目的で塗布されることが多いが、この皮膜が熱処理時に残存すると、リンが鋼中に拡散し、炭素と置き換わるために脱炭層が生じ、ここに水分が存在すると、脱炭部が選択的に腐食され、境界で亀裂が発生し、水素脆性割れを促進する影響が出てしまう。このため、ボルト等遅れ破壊が問題になる製品については、JIS規格でも、熱処理前のリン酸塩皮膜の除去が規定されている。
浸炭が遅れ破壊に影響する理由は、浸炭処理の条件次第で脱炭層を作ってしまう可能性があること以外に、浸炭層と芯材の間に、素材の強度の境目が生まれ、その強度の境目に応力と水素が集中してしまうことも挙げられている。
(5)研削割れ
研削割れは、高周波焼き入れ材に見られる割れであり、研削後に線状または亀甲状に割れるものである。線状の割れは、研削熱による熱膨張が原因となり150℃程度の低温で発生するため、研削部の温度をできるだけ下げることが対策となる。亀甲状の割れは、研削による温度上昇の他、偏析による圧縮残留応力の偏りも原因となるため、焼き戻しパラメータを調整することにより軽減することもある。特に浸炭材に高周波焼き入れを実施した場合、網状にセメンタイトが残存していることが原因となる場合があり、より浸炭層を深くするように浸炭条件を変えることにより、研削割れは軽減する。
奥野技術士事務所 代表 大学院修士課程(金属工学専攻)修了後、大手鉄鋼メーカーに入社。主に鉄鋼製造の現場において操業技術管理、設備管理、品質管理を担当し、その後、製品企画、プロセス技術開発、技術企画、品質保証業務(QMS品質管理責任者)を経験。2021年に退社し技術士事務所を設立、金属製品製造における品質管理、および航空宇宙製品の品質保証について、現場目線での再発防止の仕組みづくりを積極的に推進している。 現在、公財)新産業創造研究機構の航空ビジネス・プロジェクトアドバイザー、産業技術短期大学非常勤講師を務める。 |
![]() |