第3回 金属材料 疲労と材料強化
技術士の福﨑先生による機械設計者向けの金属材料に関する連載を全4回でお届けいたします。
第3回は「疲労と材料強化」です。
1 疲労破壊におよぼす影響
疲労破壊には起点と割れの進行と最終破断という3つの段階に分けることができる。そして疲労強度向上とは主に起点と割れの進行をできる限り少なくすることである。最終破断について残念ながら有効な対策は難しい。起点と割れの進行について細かく対策を分けることもあるが、強度的な要因や不純物介在物など起点にも割れの進行にも関係する要因もあるので、特に区別しない考え方もある。
疲労破壊におよぼす材料的、冶金的影響はたくさんあるが、大きく分けるとよい影響と悪い影響がある。よい影響は材料を硬く強化することなどがあり、悪い影響は不純物介在物や溶接欠陥などがある。これをまとめて表1に示す。
表1 疲労破壊におよぼす影響
良い影響 |
悪い影響 |
• 硬さ向上 • 圧縮残留応力付与 • 表面粗さ滑らかにする • 材料強化を行う • 応力値を下げる |
• 応力集中がある • 不純物介在がある • 偏析がある • 内部欠陥がある • 脆性的である |
表1の内容は疲労破壊に限らず金属材料を強化したり長期間使用する時などに注目される内容でもある。基本的な方針としては材料を強く強化して、欠点をできるだけ減らすことである。
硬さなど良い影響も、不純物介在物など悪い影響も、どちらもある程度の上限や下限がある。その中で最適な材料設計を行う必要がある。
2 不純物介在物
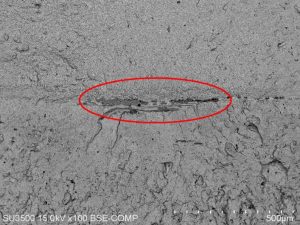
図1 不純物介在物の起点の例
不純物介在物は少ない量でも金属材料の強度を大きく下げ破壊の起点になるものである。そして多くの金属材料では不純物介在物を出来る限り減らす努力が行われている。不純物介在物は主に含有量、サイズ、分布状態などで評価される。具体的な物質としては酸化物、硫化物などがある。不純物介在物が原因で疲労破壊が起きた例を図1に示す。
また、不純物介在物ではないが溶接欠陥やダイカストの引け巣なども材料中の欠陥となる。これらは材料の中でボイドや空孔となる。不純物介在物と異なり物質として存在しないため、EDSによる破面観察では跡が残らない。しかし、ボイドや空孔もサイズや分布が多くなるほど疲労破壊の起点になりやすくなる。ボイドや空孔は材料内部の欠陥ではあるが、その多くは断面組織観察などで観察できる。また製品の品質検査として超音波検査などの非破壊検査で評価することもある。
この他に疲労破壊の起点になるものとして表面のすべり帯、キズ、製品形状による応力集中、腐食などがある。
鉄鋼材料の不純物介在物の評価方法はJIS G0555鋼の非金属介在物の顕微鏡試験方法などがある。ここでは非金属介在物(不純物介在物)の種類、サイズ、分布などの評価方法について記載されている。
不純物介在物を減らす努力は絶えず行われているが、全くゼロにすることは実用的にとても困難である。そしてこれらが材料中に存在しても、すぐに疲労破壊の起点になるわけではない。特に問題視される時は不純物介在物が大きく、量も多い時である。
3 硬さと残留応力
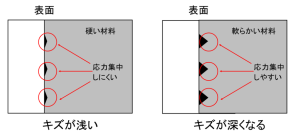
図2 硬さの影響の模式図
疲労破壊におよぼす影響として硬さと残留応力がある。硬さとは表面に異物がぶつかった時の変形抵抗と表すことができる。一般的な傾向として硬い材料は引張応力なども強い。そして硬い材料ほど疲労にも強くなりやすい。硬い材料は表面欠陥や応力集中が起こりにくいからである。反対に軟らかい材料はキズがつきやすい。そのため軟らかい材料は応力集中が起こりやすい。この模式図を図2に示す。
もちろん硬さを上げるほど材料の伸びや靭性が低下するので硬さの限度はあるが、疲労強度を高めるために硬くすることはよく行われる。
そして硬さは表面にできるキズだけでなく、き裂の進行にも関係する。これも硬さの限度はあるが、焼なまされた材料よりも硬い材料の方がき裂の進行が遅くなる。ストライエーションなどのき裂進行では、き裂先端の微小な塑性変形が起きている。そのため塑性変形は硬い材料の方が起こりにくく、軟らかい材料の方が起こりやすい。
表面のキズについては材料の最表面、き裂進行はある程度の深さまでの硬さが影響する。最表面は硬さというより耐摩耗性として評価することが多いかもしれない。き裂進行が影響する深さというと浸炭や高周波焼入れのような表面硬化処理がある。この場合、表面からどの程度まで硬さが保持されているかを硬化深さとして評価する。
残留応力は見た目ではわからないが、材料の性質としてとても重要である。残留応力とはとくに外から応力を負荷していない状態でも、材料自身に応力がかかっている状態である。そして材料の一部を切断すると残留応力が解放されて変形する性質がある。具体的には熱処理や溶接後のひずみなどがある。そして残留応力には圧縮残留応力と引張残留応力がある。
圧縮残留応力とは材料にき裂が入った時にき裂を押さえつけるように材料自身が作用する。き裂進展を材料自身が応力で押さえつけることになるので、き裂進展が起こりにくくなる。つまり、圧縮残留応力は疲労破壊を防ぎ強度を高める働きがある。
また、圧縮残留応力のこのような作用は疲労破壊のき裂を抑えるだけでなく、一般的な切削や切断加工などでも起こる現象である。この時は切削工具を押さえつけてしまうので、切削加工は困難になる。
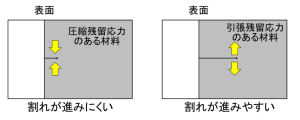
図3 残留応力の模式図
反対に引張残留応力とは材料にき裂が入った時にき裂を広げるように材料自身が作用する。これはき裂進展を促進するので、疲労破壊が大きく進行する。そのため引張残留応力は疲労破壊を起こしやすくする危険な残留応力となる。疲労破壊に限らず、引張残留応力は材料にとって有害な残留応力として扱われる。圧縮残留応力と引張残留応力について図3に示す。
4 材料強化方法
金属材料を強化することは塑性変形を起こしにくくすることでもある。そして金属材料の塑性変形には転位という原子レベルの欠陥が移動することによって行われる。そのため、この転位を動きにくくすることが金属材料を強化することになる。なお、転位は上述の不純物介在物やボイドと異なり、疲労破壊の起点になることはない。金属材料を硬く強くする方法はたくさんあるが、原理的に大きく4種類に分けることができる。これを表2に示す。
表2 金属材料の強化方法
強化方法 |
実際の強化方法 |
固溶強化 |
他の元素を混ぜることなど |
転位強化 |
鍛造や圧延などの加工をするなど |
粒子分散強化 |
硬い物質を微細分散させるなど |
結晶粒微細化強化 |
結晶粒を微細にするなど |
固溶強化とは異なる元素を添加することである。金属の原子サイズは種類によって変わるので、別の元素を添加すると結晶構造がひずむ。これによって材料が強化される。
固溶強化を詳しく見ると置換型固溶体と侵入型固溶体に分けられる。置換型固溶体とはもともとの結晶構造の位置にある金属元素と添加した合金元素が入れ替わることである。元のサイズより大きい元素ではまわりの結晶構造を圧迫し、元のサイズより小さい元素では結晶構造が収縮される。
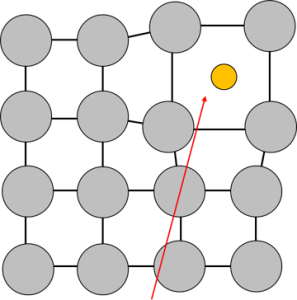
図4 侵入型固溶体の模式図
侵入型固溶体とはもともとの結晶構造のすき間に入り込むことである。これはある程度小さい元素でないとできないので、主に炭素や窒素などを添加した時にあてはまる。そして置換型固溶体と侵入型固溶体では侵入型固溶体の方が材料が強化されやすい。侵入型固溶体の模式図を図4に示す。
転位強化とは学術的な呼び名であるが、一般的な鍛造や圧延などの加工硬化がその代表例である。他にも例えばワイヤーや板を繰返し曲げ加工すれば、その場所がだんだん硬くなることは日常的にみられることである。これも一種の転位強化である。
転位強化は名前の通り転位が関係する強化方法である。転位はすべり面という転位が動くことができる特定の原子面を移動している。すべり面とは結晶構造のなかで最も原子が密になっている面(体心立方格子の(110)面、面心立方の(111)面)などである。
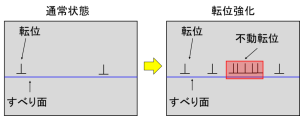
図5 転位強化と不動転位の模式図
そして転位は材料の中にある程度の数が存在している。応力負荷などの加工を行うと多くの転位がすべり面上を移動するようになる。この時、強い応力によってたくさんの転位同士がからまり動けなくなる状態を不動転位とよぶ。不動転位ができると、他の転位はそこを通ることができないので転位の動きを妨げるものとなる。この不動転位が材料中にたくさんできることで材料は硬く強化される。不動転位の模式図を図5に示す。
また、引張試験で降伏応力や0.2%耐力を過ぎた後の塑性変形領域では応力が上昇する傾向が見られる。この応力上昇も転位強化によるものである。
粒子分散強化とは材料中に硬い材料を添加して強化することである。この考え方は金属材料に限らず多くの構造材料に見られる。ただし、粒子分散強化の効果を最大限に引出すためには最適な粒子サイズや分布が必要である。
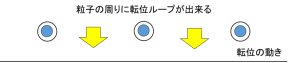
図6 粒子分散強化のオロワン応力の模式図
粒子分散強化では、単に硬い粒子を材料中に分散させるのではなく、粒子と転位と関係性が重要になる。転位とはナノレベルの現象なので、そのためには粒子もナノレベルであることが好ましい。
転位が金属材料中を移動している時に硬い粒子に接触すると、転位は簡単に硬い粒子を通ることができない。そして、転位は粒子の周りに張出すような状態になる。ここからさらに転位が無理やり粒子を通り抜けようとすると、粒子の周りに転位ループとよばれるものを残して転位は粒子を通り抜ける。この転位ループはオロワンの機構やオロワン応力と呼ばれている。この模式図を図6に示す。これによって粒子分散強化が効果を発揮する。そして粒子分散強化は粒子の間隔が狭いほど大きくなる。粒子分散強化は時効析出硬化などでよく行われている。
結晶粒微細化による強化とは金属材料の結晶粒を細かくすることである。結晶粒微細化は他の強化方法と異なり、結晶粒を細かくすることによるデメリットがあまりないので多くの金属材料で積極的に行われている。
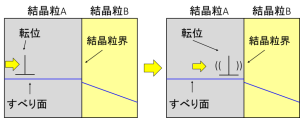
図7 結晶粒界と転位の関係
結晶粒微細化の原理として隣り合う結晶粒のすべり面と転位が関係している。1つの結晶粒の中で結晶構造は同じ向きをしているが、別の結晶粒では結晶構造の向きが異なっている。つまり、結晶粒が多くあるとそれだけいろいろな向きの結晶構造があると言うことができる。そして結晶構造の向きはすべり面の向きとも関係がある。結晶構造の向きが異なるとすべり面の向きも異なってくる。
これは転位の動きにも関係してくる。転位は結晶粒が多くても、それを通過して最終的には材料表面まで移動する。しかし、結晶粒界に到達して、となりの結晶粒に移動する時はすべり面の向きが異なるので、結晶粒界を通過するためには大きな力が必要になる。そのため転位にとって結晶粒界そのものが障害物となる。結晶粒界が多いことは結晶粒が細かいことと同じである。そのため結晶粒を細かくすること(結晶粒界を多くすること)で材料強化が行われる。
結晶粒微細化と材料強化についてはホールペッチの式と呼ばれる関係式がある。これによって結晶粒径と降伏応力が関係づけられている。
5 鍛造
金属材料を強化する方法としては上記の4つがある。ただし、1つ1つの方法を個別で行うよりも複数の強化方法を合わせて行うこともある。実際に鉄を強化する具体的な方法としては表3のように多くの方法がある。
表3 鉄を強化する方法
方法 |
内容 |
炭素を添加する |
鉄にとって炭素はとても重要な元素。炭素量が多いほど硬くなる。 |
鍛造などで加工する |
古くは刀鍛冶に代表される方法。鉄を叩いて強くする方法。 |
焼入れ(熱処理)をする |
これも刀鍛冶から行われている方法。 真赤に加熱した鉄を冷やして硬くする。 |
クロムなど 合金元素を添加する |
鉄を硬くする作用のある合金元素を添加する。 |
圧延と熱処理をする |
適切な圧延と熱処理によって均一状態の鉄板を作ることができる。 |
炭素やクロムなど合金元素を添加する方法、鍛造など加工する方法、熱処理などがある。そして、これらを組み合わせることもある。この中で本稿では鍛造について述べる。
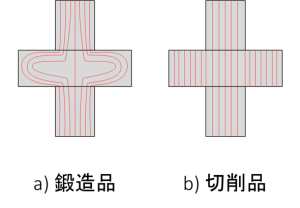
図8 鍛造による鍛流線の模式図
鍛造は古くは刀鍛冶に代表される金属加工方法である。刀を作る時は鉄を叩いて硬く強化している。そして、鉄を叩いて強くする手法は現在でも鍛造加工として行われている。鍛造は転位強化であり、鍛造によって金属材料の中に転位がたくさん導入される。また、結晶粒径も鍛造によって細かく加工されるので結晶粒微細化の効果もある。
そして鍛造の大きな特徴は加工によって形成される鍛流線と呼ばれる独特の組織にある。鍛流線とは製品全体を繊維状に流れる組織のことである。鍛流線の模式図を図8に示す。一般的な繊維組織はワイヤーなど単純な形状でも見られるが、鍛流線はクランクシャフトなど複雑な形状全体にわたって繊維組織を形成することができる。
クランクシャフトのような複雑な形状の製品は応力集中を起こしやすい場所が生じやすい。これをもし切削加工で成形すると応力集中している場所が弱く疲労破壊の起点になりやすいが、鍛造加工された製品では形状的に応力集中しやすい場所でも、鍛流線の影響によって切削加工品よりも疲労破壊の起点が起こりにくくなる。これが鍛造品が強い理由である。
福﨑技術士事務所 福﨑 昌宏 2005年 千葉工業大学大学院 工学研究科 金属工学専攻を修了。 同年 金属加工メーカー、2013年に建設機械メーカー 研究開発部に入社。2017年に技術士(金属部門)取得。2019年4月より独立開業。 金属材料の破損・不具合に関する分析調査を専門とし、これまでに歯車など機械部品の材料開発や品質改善、疲労破壊の破面分析などについてコンサルを手掛ける。同時に若手の技術者向けの金属材料に関する講演や執筆を多数行う。 |
![]() |