第4回 金属材料 疲労と鋼の熱処理
技術士の福﨑先生による機械設計者向けの金属材料に関する連載を全4回でお届けいたします。
第4回は「疲労と鋼の熱処理」です。
1 疲労と熱処理
疲労破壊に強い金属材料を作るために様々な材料強化が行われている。そして、金属材料にとって熱処理は強度を高めたり組織を改善するために不可欠な加工である。金属材料に熱処理を行う目的はさまざまであるが、鉄鋼材料では大きく4種類に分かれている。これを表1に示す。
表1 鉄鋼材料の熱処理
名称 |
目的 |
処理方法 |
焼なまし(焼鈍) |
内部応力の除去 軟化 |
A1、A3から30~50℃上処理後徐冷 500~600℃処理後徐冷 |
焼ならし(焼準) |
微細組織 鋳造組織や繊維組織の改善 |
A3、Acmから40~60℃上処理後空冷 |
焼入れ |
硬質化、強度向上 マルテンサイト組織 |
A1、A3から30~50℃上 処理後急冷 |
焼戻し |
焼入れ硬さの調整 残留応力の除去 |
150~200℃処理 |
単純に鉄を加熱すると焼なましのように柔らかくなる傾向がある。これには加工ひずみの開放や再結晶のような現象が起こるためである。ただし、焼なましの温度を高くしすぎたり、保持時間を長くしすぎると結晶粒が粗大になり機械的性質が損なわれることもある。
焼ならしとは組織の改善を目的に行われる熱処理である。処理温度としては高めになるが、均一な微細組織にするために行われる。また、焼なましよりも冷却速度が早くなる。
焼入れとは高温から水や油などに入れて急冷することで鉄を硬く強くすることである。これにはマルテンサイトという非常に硬い鉄の組織が焼入れで形成されるからである。
焼戻しとは焼入れたばかりの鉄は硬くて脆いので硬さを調整して割れにくくする処理である。焼戻しは焼入れより低い温度で行われる。また鉄鋼の種類によってさまざまな温度(低温焼戻し、高温焼戻しなど)で焼戻すことがある。
2 疲労とマルテンサイト
鉄鋼の熱処理において焼入れ、マルテンサイト組織は非常に重要である。鉄鋼を強化するために鍛造など色々な加工方法が行われるが、焼入れによるマルテンサイト組織によって鉄は非常に硬く強化される。
焼入れはどんな鉄にも起こる現象ではない。マルテンサイト組織は適切な炭素量の鋼を高温から急冷することによって出来上がる。もともと鉄の中の炭素量が増えれば硬くなる傾向はあるが、マルテンサイト組織はさらに鉄を硬く強化することができる。フェライト組織やパーライト組織と比べてマルテンサイト組織は非常に細かい組織となっているのが特徴である。
鉄は温度によって結晶構造が変わる性質がある。これは全ての金属に当てはまることではなく、鉄の他にチタンなど一部の金属に見られる特徴である。
室温など普段我々が扱っている鉄は体心立方格子のフェライトと呼ばれる。そして温度が上昇し、912℃以上になると面心立方格子のオーステナイトになる。さらに温度が上がり1394℃になると再び体心立方格子のδ(デルタ)鉄になる。そして1538℃になると融点になり鉄は溶解する。この様子を図1に示す。
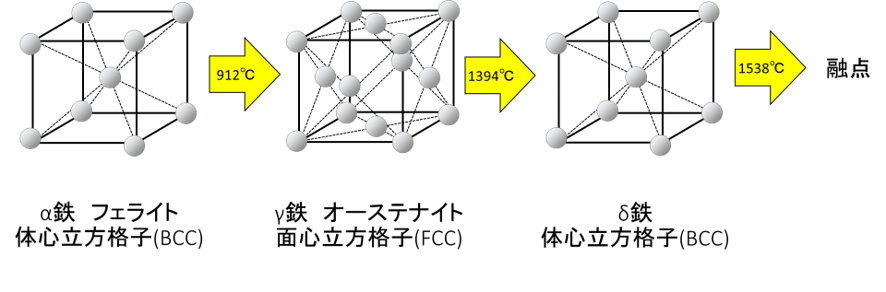
図1 鉄の結晶構造と温度の関係
鉄の結晶構造の変化のなかでマルテンサイトに関係するのはフェライトとオーステナイトである。焼入れは高温から急冷することだが、高温とは鉄をオーステナイトになるまで加熱することである。そして急冷とはオーステナイトからフェライトに素早く冷却することである。
もちろん単に鉄を加熱冷却するだけではマルテンサイト組織にはならない。そこで炭素が関係してくる。マルテンサイト組織を作るためには適切な炭素量が必要である。オーステナイトを急冷する時に炭素があると、フェライトに入り込み鉄を非常に強化するのである。
熱処理や組織を扱う時に基本となるものに鉄-炭素系状態図がある。これは鉄鋼材料が温度や炭素量によってどのような組織を形成したり、どの程度の温度で熱処理を行うのか設計する時の目安になる。鉄炭素系状態図を図2に示す。
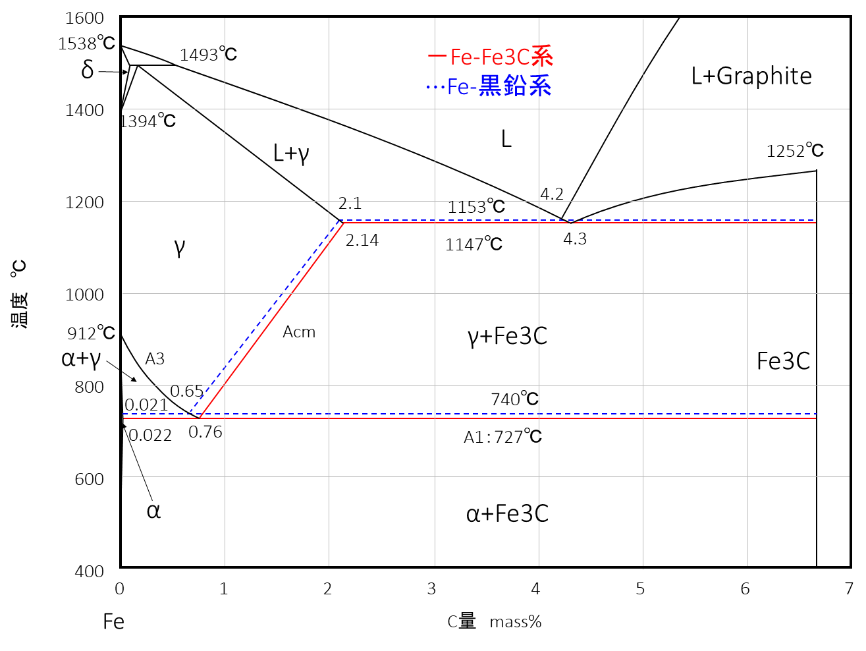
図2 鉄炭素系状態図
状態図を見る時に注目する温度としてフェライトとオーステナイトが変わるA1(727℃)や、オーステナイト単相となるA3やAcmなどの温度がある。鉄鋼を焼入れするためにはA1やA3よりも高い温度にしなければならない。なぜなら焼入れとはオーステナイト組織からフェライト組織に急冷することで作られるからである。
そして、状態図は温度だけではなく炭素量も重要な要因である。鉄に炭素を入れると硬くなる傾向があるが、それは状態図からも見られる。鉄の中の炭素量が増えるとフェライトからパーライトが増えていく。そしてさらに炭素が増えるとセメンタイトという非常に硬い組織も表れる。
炭素量0.02%未満の鉄は純鉄と呼ばれる。フェライトの最大炭素固溶量である。純鉄は軟らかい鉄である。0.02%から2.14%の炭素量の鉄を鉄鋼と呼ぶ。2.14%はオーステナイトの最大炭素固溶量である。そして2.14%以上の炭素量の鉄は鋳鉄と呼ばれる。
ここで状態図に注目するとマルテンサイトという記載がない。しかし、現実的にマルテンサイトは存在しており、広く使われている鉄鋼である。実は状態図は急冷した時の組織を記載していないのである。状態図は平衡状態という、その温度や炭素量で安定した状態を表している。体感的には焼なましのようにゆっくり冷却した時の状態を表しているのである。
マルテンサイトは硬いという印象があるが、実際の硬さデータを見ると炭素量が多くなるほど硬くなる傾向がある。焼入れは最低限の炭素があれば可能だが、炭素が少なければ硬さの上昇量も少ない。そして炭素を増やせば増やすほど硬さが増加するのだが、およそ0.6~0.7%程度で頭打ちになる。この様子を図3に示す。
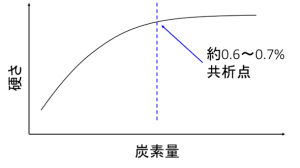
図3 マルテンサイトの硬さと炭素量の関係
鋼の焼入れは非常に重要なため、焼入れに関係する合金元素も重要である。焼入れは急冷することが重要だが、他にも合金元素の影響もある。同じ冷却方法でも焼入れしてマルテンサイトになりやすくなる合金元素もあれば、反対にマルテンサイトになりにくくなる合金元素もある。マルテンサイトになりやすい合金元素を焼入れ性が良いという。反対は焼入れ性が悪いという。
焼入れ性が良い合金元素としてクロム、モリブデン、バナジウム、タングステン、ニッケルなどがある。これらは合金鋼や特殊鋼によく用いられる合金元素である。そのため、S45Cなどの炭素鋼よりもクロムモリブデン鋼SCMなどの合金鋼の方が焼入れ性が良いのである。反対に焼入れ性が悪い合金元素はコバルトやジルコニウムなどである。
鋼の焼入れ性を評価する図として等温(恒温)変態曲線(TTT曲線)と連続冷却曲線(CCT曲線)がある。これを図4に示す。TTT曲線はオーステナイトから冷却してある温度に保持した時にどのような組織になるか表したグラフである。CCT曲線はオーステナイトからさまざまな冷却速度で冷却した時にどのような組織になるか表したグラフである。どちらのグラフでも素早く冷却すればマルテンサイトになり、ゆっくり冷却したり、高温で保持するとパーライトになる。
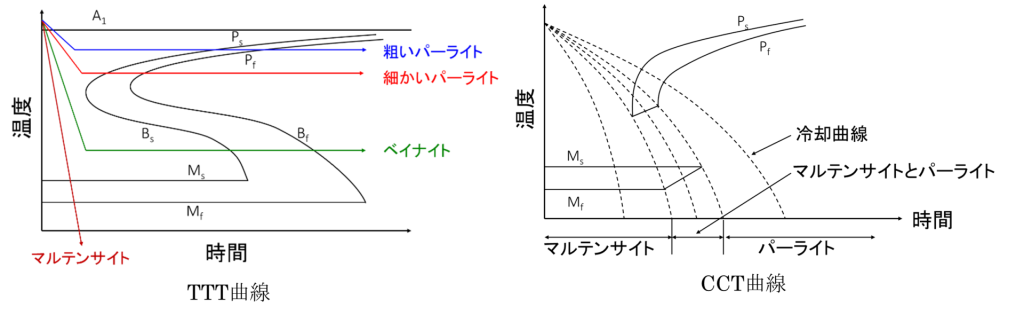
図4 TTT曲線とCCT曲線
TTT曲線やCCT曲線は様々な鋼種に対して描かれている。実際の焼入れにおいて冷却速度を求める時に参考にされている。Msはマルテンサイトスタート(マルテンサイト化が始まる温度)、Mfはマルテンサイトフィニッシュ(マルテンサイトが完了する温度)である。また、Pはパーライト、Bはベイナイトという鉄鋼材料の組織である。
3 鋼の表面硬化処理
熱処理によって鋼の表面を硬くする方法はいくつかある。表面硬化処理はそれぞれ硬さ、原理、硬化深さなどが異なる。これを表2に示す。
表2 鋼の表面硬化処理
名称 |
硬化深さ |
特徴 |
浸炭 |
数mm |
表面から炭素を拡散させて焼入れして表面をマルテンサイトにする。 |
高周波焼入れ |
数mm |
表面を高周波で加熱して焼入れして表面をマルテンサイトにする。 |
窒化 |
数十~数百μm |
表面から窒素を拡散させて窒化鉄の層を形成する。 |
ショットピーニング |
数百μm |
鋼球をぶつけることで表面を塑性加工させて、圧縮残留応力を付与する。 |
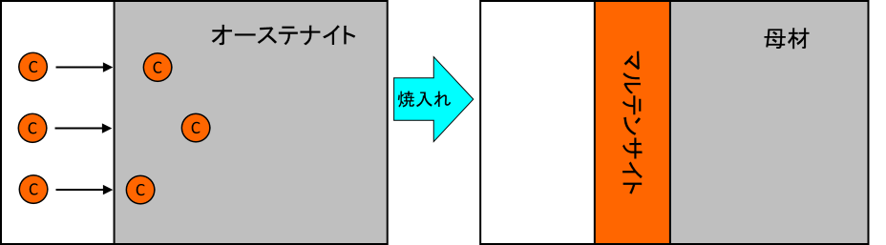
図5 浸炭の模式図
浸炭は鋼をオーステナイト温度まで加熱し表面から炭素を拡散させて焼入れてマルテンサイトにする。浸炭する時の鋼は後から炭素を拡散させるので、炭素量は低めの鋼(はだ焼鋼とも言う)が使用される。浸炭によって表面の炭素量は0.8~1.0%程度になる。浸炭の模式図を図5に示す。
浸炭用の鋼としては炭素量0.2%程度の鋼が用いられる。炭素鋼、合金鋼どちらにも浸炭用の鋼はあるが、合金鋼の方が焼入れ性がよい。
表面からの硬さと炭素量のプロファイルではどちらも表面が最も高く、内部に行くに従い低下していく。硬化深さとしては数ミリ単位である。最終的には元々の硬さや炭素量に落ち着く。
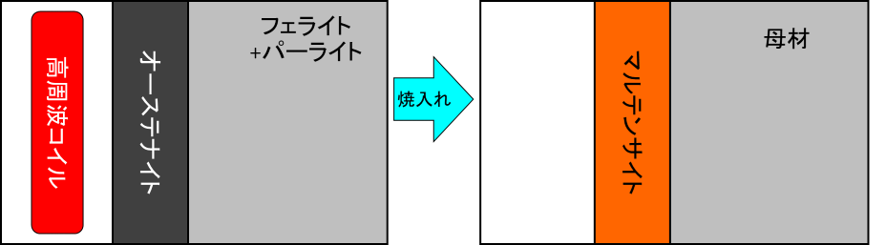
図6 高周波焼入れの模式図
高周波焼入れは鋼の表面を高周波コイルでオーステナイト温度まで加熱し焼入れてマルテンサイトにする。浸炭と異なり、後から炭素を拡散させないので材料自身の炭素量を利用してマルテンサイトにする。そのため、浸炭よりも炭素量の高い鋼が使用される。高周波焼入れの模式図を図6に示す。
炭素量としては0.4~0.5%程度の鋼が用いられることが多い。高周波焼入れは炭素鋼、合金鋼の他にも多くの鋼で行われている熱処理である。表面の硬さや硬化深さは浸炭と同様の硬さや硬化深さを得ることができる。
浸炭や高周波焼入れに適用されるのは歯車やシャフトなど表面同士が接触する部品が多い。表面で金属同士が接触するので硬い材料が好まれるのである。
また浸炭と高周波焼入れの違いは加工方法や生産時間にある。浸炭は主に浸炭炉の中にある程度の量の製品を一度に入れて数時間かけて処理するが、高周波焼入れは1品ずつ高周波コイルにセットして数分で処理を行う。
そして浸炭の炭素の拡散時間や高周波焼入れの加熱時間などによって硬化深さが変わる。製品サイズ、生産量、硬化深さなどによって浸炭と高周波焼入れの生産性が変わってくる。
窒化は浸炭や高周波焼入れよりも低いフェライト温度域(500℃程度)で行われる。窒化はマルテンサイトではなく窒化鉄という硬い化合物が表面に形成され、その下には拡散層という層が形成される。窒化鉄はマルテンサイトより硬いが硬化深さは非常に薄い。拡散層まで含めても数百μm程度である。また、熱処理温度も浸炭や高周波焼入れより低いので熱によるひずみも少ない。窒化の模式図を図7に示す。
窒化は主にアンモニアガスが用いられる。そして窒化処理に数十時間かかるのが欠点である。主に表面の耐摩耗性向上として行われることが多い。窒化用の鋼としてアルミニウムクロムモリブデン鋼のSACMがある。
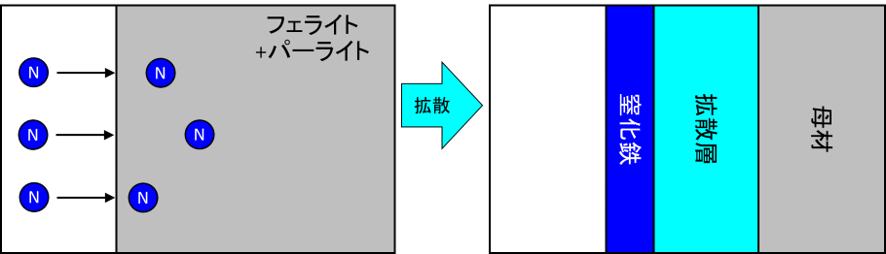
図7 窒化の模式図
もちろんSACM以外の鋼を窒化することはあるが、アルミニウムとクロムを含んでいるSACMはとても高強度の材料になる。
ショットピーニングは熱処理ではないが、疲労強度向上の加工としてよく使われる。ショットピーニングは表面に無数の鋼球などを高速で衝突させる加工である。この結果、表面は凸凹に塑性変形されるので加工硬化を起こし、さらに圧縮残留応力が付与される加工である。ショットピーニングの模式図を図8に示す。
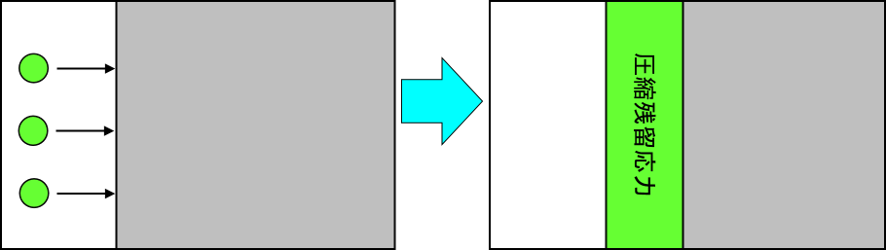
図8 ショットピーニングの模式図
圧縮残留応力は材料の奥深くまでは入りにくく、比較的表面の浅い数百μm程度の層である。ただし、ショットピーニングは単独で加工されることもあるが、浸炭と合わせて加工されることもある。浸炭によるマルテンサイトにさらに圧縮残留応力を付与するのである。通常の浸炭にもある程度の圧縮残留応力はあるのだが、ショットピーニングによってさらに圧縮残留応力を大きく向上することができる。これによって疲労強度の高い材料を作ることができる。
4 疲労と残留オーステナイト
鋼を急冷すると焼入れでマルテンサイトになるが、浸炭のように炭素量が高くなると100%マルテンサイトにならず室温でもオーステナイトのまま残るようになる。これを残留オーステナイトという。残留オーステナイトは決して冷却速度が遅いことや焼入れの不具合で生じたものではない。
先述のTTT曲線やCCT曲線でもマルテンサイトになるには冷却速度や温度が重要である。その他にマルテンサイトに関係する温度としてマルテンサイトが始まる温度(Ms点)とマルテンサイトが完了する温度(Mf点)がある。このMs点とMf点は炭素量が増加すると温度が低下する傾向がある。そして浸炭のように高炭素の領域ではMf点が室温以下になるのである。焼入れにおいて冷却するために油や水を使用しても室温以下に冷却することは出来ない。これが残留オーステナイトが生成する理由である。
残留オーステナイトは周りのマルテンサイトに比べれば軟らかい材料である。そして残留オーステナイトの性質として応力負荷などによってマルテンサイトに変化することがある。残留オーステナイトからマルテンサイトに変化するときに体積変化を伴うので、精密な製品には嫌われている。ただし、残留オーステナイトはサブゼロ処理という液体窒素などの室温以下に冷却することでマルテンサイトに変化させることができる。
しかし、残留オーステナイトは必ずしもトラブルばかりではない。一定の残留オーステナイトは疲労強度に対して効果的に働くことが見られる。硬いマルテンサイトの中にほどほどの軟らかさと靭性となる残留オーステナイトがいることで、製品全体的な疲労強度が向上するという考えである。もちろん残留オーステナイトは軟らかいので、多すぎたら強度低下につながるし、少なすぎても効果が低い。適切な残留オーステナイトによって疲労強度の向上の可能性もある。この様子を図9に示す。
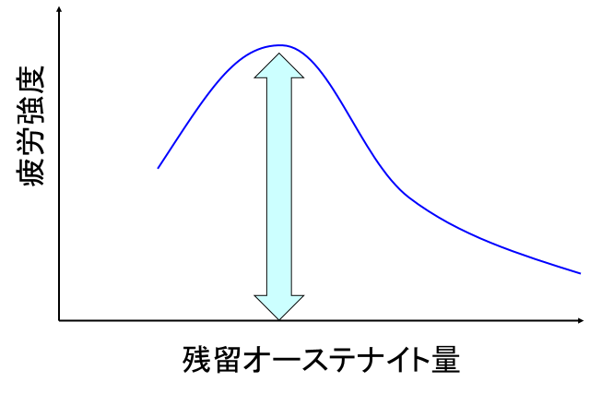
図9 残留オーステナイトと疲労強度の関係
疲労強度向上のための対策はいくつかあるが2つの方針がある。1つは高強度材料を突き詰めることである。もう1つはほどよい強度と靭性のバランスをとることである。高強度の材料を作るためには浸炭や高周波焼入れとともにショットピーニングや表面研削などを合わせて行い硬さ、圧縮残留応力、表面粗さなどを向上させることである。
一方、強度と靭性のバランスをとるためには浸炭や高周波焼入れを行いつつ、適切な残留オーステナイトを得ることである。
これは、どちらの方法が優れているとか適切であるということではない。製品に求められる仕様やコストなどを考慮して決めることである。
福﨑技術士事務所 福﨑 昌宏 2005年 千葉工業大学大学院 工学研究科 金属工学専攻を修了。 同年 金属加工メーカー、2013年に建設機械メーカー 研究開発部に入社。2017年に技術士(金属部門)取得。2019年4月より独立開業。 金属材料の破損・不具合に関する分析調査を専門とし、これまでに歯車など機械部品の材料開発や品質改善、疲労破壊の破面分析などについてコンサルを手掛ける。同時に若手の技術者向けの金属材料に関する講演や執筆を多数行う。 |
![]() |